RTT’s Ultimate Custom Spray Booth Design Challenge #3
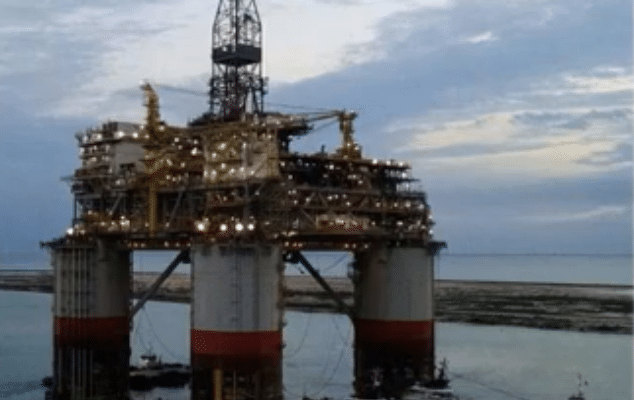
Spray booth Design challenge:
Kiewet Corporation, one of North America’s largest and most respected engineering and construction organizations, needed large scale parts needed to be blasted and coated without being moved. Once blasting began, the coating process would follow 5 days later, requiring a humidity and temperature controlled environment to minimize flash rusting.
RTT Solution:
Custom 135’w x 60’h x 193’d MegaBooth
This booth required a 2-in-1; a temperature and humidity-controlled spray and blast booth. RTT created a MegaBooth designed for blast and paint modes along with temperature and humidity controls. We had dedicated recirculation fans, exhaust fans, dust collectors, and water chilled AMUs to supply air to the booth and allow for crossflow air movement. Weighted curtains allowed the booth to be sectioned off into 3 independent zones with 24,000 lumen LED fixtures in each zone. The location of the booth required the design to withstand hurricane force winds. This was tested by hurricane Harvey in 2017, which resulted in no damage to the spray booth.

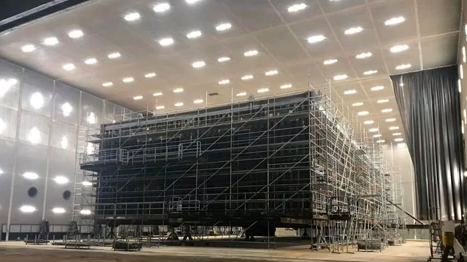
Why is a spray booth required?
- A spray booth is needed to confine and evacuate atomized particulate and vapors within a restricted environment.
- Prevent overspray and volatiles from migrating and causing unsafe conditions or contamination outside of the designated spray area
- Provide a clean environment in which to paint and minimize contamination in the coated product
- Prevents a combustible combination of flammable vapors and air
- Required by OSHA and NFPA

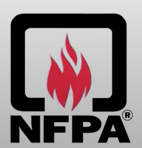
A spray booth consists of:
- A work area/compartment where spraying takes place
- An exhaust chamber with filter media for collecting particulate
- An exhaust fan and motor ducted to the exterior of the building
- A spray booth can be open face, enclosed, or pressurized
Spray booths are typically designed by the direction of the airflow. Crossdraft booths intake air through filters in the product doors. The clean, filtered air is drawn through the booth and exhausted through a filter system at the opposite end. Downdraft booths take in fresh air from the cleaner upper levels of the shop through a filtered booth ceiling. The filtered air is drawn down and away from the product into the filtered exhaust pit located in the floor.
Side Downdraft booths intake air from the cleaner upper levels of the shop through a filtered booth ceiling. The filtered air is drawn down and away from the product through exhaust filters at the floor level, along both sides.
Modified Downdraft booths intake fresh air from the cleaner upper levels of the shop through a filter bank located in the booth ceiling, near the product doors. The filtered air is drawn down through the booth to an exhaust filter system at the opposite end.
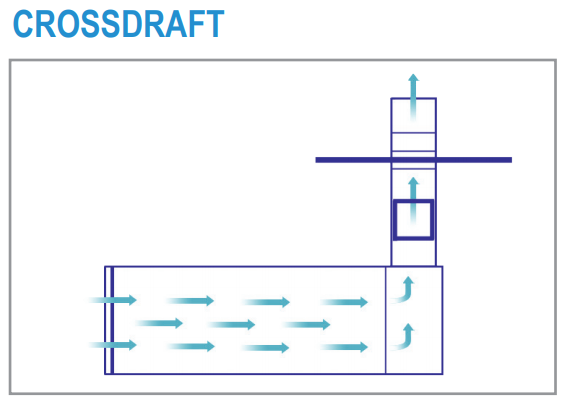

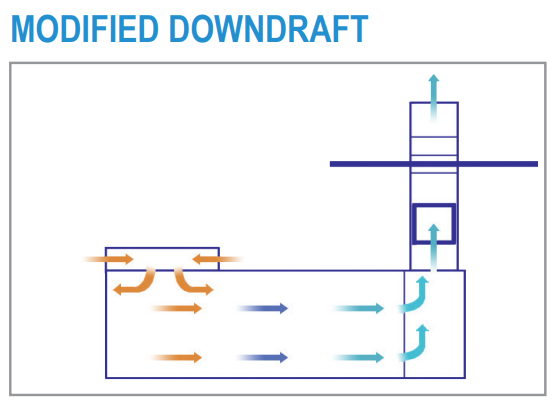
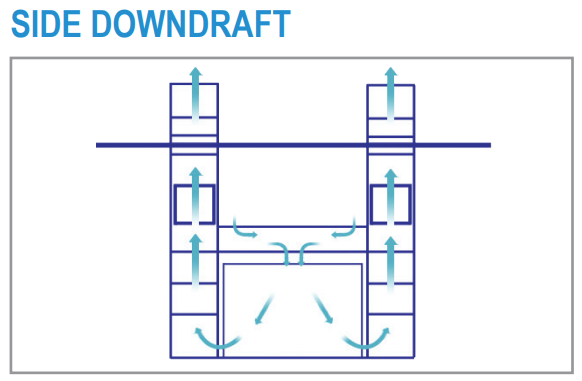
Some quick highlights that we use to design our spray booths that are determined by OSHA and NFPA:
- Shall not be less than 100 linear feet per minute
- Electrostatic spraying may not be conducted at not less than 60 linear feet per minute
- The required airflow velocities range from 50-250 linear foot per minute (FPM) into the openings of a spray booth
- Dilute solvent vapor to at least 25 percent of the lower explosive limit
- The concentration of the vapors and mists in the exhaust stream of the ventilation system shall not exceed 25 percent of the lower flammable limit
RTT Standard Designs:
We offer a wide range of standard booths that are pre-engineered, or “-S” booths. These booths have been drawn, detailed, the established customer packet has been set, and can typically be delivered within 10 days of ordering.

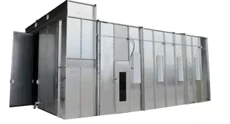
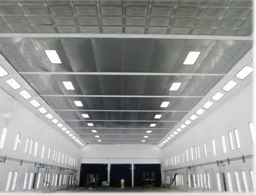
Ready for a quote
Have questions or need help in choosing the right custom RTT booth for your needs? Reach out and we will be happy to assist you.